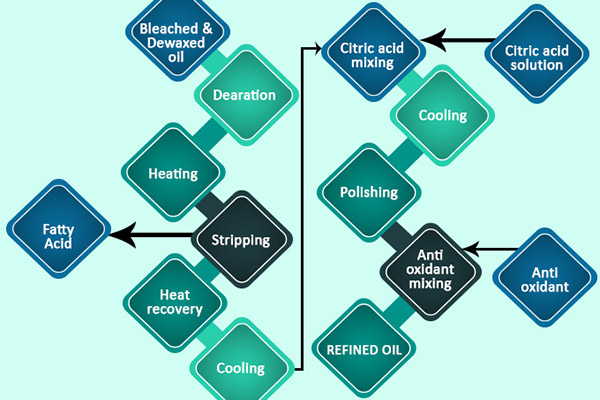
Introduction
The canola oil refining process is divided into intermittent and full continuous refining. Including deacidification, desolventization, and decolorization processes. Huatai Oil Machinery specializes in producing various vegetable oil refining equipment and has extensive experience in processing different oil equipment. Today, let’s explore the process flow of canola oil refining equipment!
Canola Oil Deacidification Process
Huatai’s canola oil deacidification process is a refining method that uses alkali to neutralize free fatty acids and remove some other impurities at the same time. There are many types of alkalis used, such as lime, organic alkali, soda ash, and caustic soda. The most widely used is caustic soda.
The alkali refining method is divided into two types: intermittent and continuous alkali refining methods. The former can be divided into two operating methods: low temperature and high temperature. The basic principle is the alkali solution reacts with the free fatty acids in the crude oil to neutralize. The reaction formula is as follows:
RCOOH+NaOH→RCOONa+H2O
In addition to the neutralization reaction, there are also certain physical and chemical effects. Here’s what happens during the process:
- Caustic soda neutralizes free fatty acids in the crude oil, forming sodium soap (soap stock), which precipitates as a colloid.
- Soap stock has a strong adsorption capacity. Therefore, a considerable amount of other impurities (such as protein, mucus, pigment, etc.) are adsorbed and precipitated by it. And even mechanical impurities are no exception.
- The free cottonpol contained in the raw cotton oil can react with caustic soda to become phenol salt. This phenol salt is more easily adsorbed and precipitated by soap stock during the alkali refining process. Thereby reducing the color of the cotton oil and improving the quality of refined cotton oil.
While neutralizing free fatty acids, neutral oil may also be saponified and increase losses. Therefore, it is necessary to select the best conditions to increase the refined oil rate.
Canola Oil Desolventizing Process
The operation of removing residual solvent from the leached oil is called “desolventizing”. The residual solvent in the oil should not exceed 50 mg/L after desolventizing.
At present, the most widely used desolventizing method in the world is steam distillation. When water vapor passes through the leached crude oil, it contacts the vapor-liquid surface, saturates with the volatilized solvent, and escapes according to its partial pressure ratio, removing the solvent. The following are the specific steps of desolventizing:
Step 1: Fill the Desolventizing Pot
Start the vacuum pump to stabilize the vacuum degree of the desolventizing system at about 7000 Pa. Suck the leached oil into the desolventizing pot, and the oil filling amount is about 60% of the pot capacity.
Step 2: Heat Oil with Steam
Turn on indirect steam and raise the oil temperature to 100℃. Introduce direct steam with a pressure of about 0.1 MPa to fully stir the oil in the pot. Then continue to use indirect steam to raise the oil temperature to 140℃, and at the same time, the desolventizing begins.
Step 3: Monitor Extraction Oil Quality
Observe the quality of the leached oil. The desolventizing time is generally about 4 hours. During this period, you need to keep the oil temperature at 140℃ and the vacuum degree at about 8000 Pa.
Step 4: Turn Off Steam
Turn off the indirect steam 0.5 hours before the end of desolventizing. The direct steam can be turned off only after the specified time.
Step 5: Cool Desolventized Oil
Pass the desolventized oil through a cooler, or cool it to 70℃ in the pot, then break the vacuum and release it as finished oil.
The equipment used when desolventizing is called a desolventizing pot. There are other auxiliary equipment, including a W-type mechanical vacuum pump or steam-water series jet pump, atmospheric condenser, air balance tank, and liquid foam collector.
Canola Oil Decolorization Process
The methods for oil decolorization include oxidation, chemical decolorization, heating, and adsorption. The most widely used method is adsorption. That is, certain substances with strong adsorption capacity (acid-activated clay, bleaching earth, activated carbon, etc.) are added to the oil. The pigments and other impurities (protein, mucus, resin, soap, etc.) in the oil are adsorbed and removed under heating.
Intermittent decolorization is a process in which the oil and adsorbent complete the decolorization process through an adsorption equilibrium in an intermittent state.
The decolorized oil is transferred to the decolorization tank through the storage tank. After heating and drying under vacuum, it is fully contacted with the adsorbent sucked from the adsorbent tank under stirring to complete the adsorption equilibrium.
Then it is cooled and pumped into the filter press by the oil pump to separate the adsorbent. The decolorized oil after filtration is collected in the storage tank and is transferred to the deodorization process by vacuum suction or oil pump. The adsorbent filter cake in the filter press is transferred to the treatment tank to recover the residual oil.
Canola Oil Deodorization Process
Canola oil deodorization is a process that uses superheated steam (under vacuum conditions) in a deodorization pot to remove the odor substances in the oil.
The principle of vacuum steam deodorization is that water vapor passes through the oil containing the odor components, and the vapor-liquid contact occurs. The water vapor is saturated with the volatile odor components and is removed according to their partial pressure ratio.
Canola Oil Dewaxing Process
The wax content of various crude oils varies greatly. For example, the wax content of corn germ oil is 0.01% to 0.04%, the wax content of sunflower oil is 0.06% to 0.2%, and the wax content of rice bran oil is 1% to 5%. Almost all vegetable oils require a dewaxing process.
At present, there are many methods for dewaxing, namely conventional method, solvent method, surfactant method, coagulant method, electrostatic method, etc. Although the auxiliary means used in various methods are different, the basic principles all belong to the category of freezing crystallization and separation. That is, by cooling and precipitating crystalline wax, the purpose of oil wax separation is achieved through filtration or other separation means.
In dewaxing, strict control of cooling rate and stirring is the key to success, which can promote the formation of crystal nuclei that are conducive to crystal growth. Of course, the cooling rate selected depends on the type of oil and the dewaxing process.
Huatai has successfully developed a canola oil and sunflower oil dewaxing technology that combines rapid cooling crystallization. Its characteristics are short crystallization and crystal growth time, neat grains, and conducive to wax filtration.
Canola Oil Filtration Process
The quality of filtration directly affects the quality of the canola oil. Huatai Oil Machinery has concentrated its technical strength to successfully develop the XTL rotary dewaxing filter at an internationally advanced level.
The machine has high filtration efficiency, automatic operation, wide application range, and greatly reduced labor intensity. Compared with the expensive imported equipment, it is more suitable for Chinese customers due to its low investment.
Conclusion
Huatai Oil Machinery operates its canola oil processing plant. integrating design, manufacturing, installation, commissioning, scientific research, sales, and after-sales service. The equipment is environmentally friendly, energy-saving, and offers high oil yield. Our professional engineer team will tailor a plan for you. Welcome to visit our factory!
Get your best price
- Engineer quick quote
- The overall delivery speed is fast
- Financial choice
- Low installation costs and cost savings

30 years+ of oil mill plant R&D
More than 56 innovative technologies